[10.10.16] Wax Heater
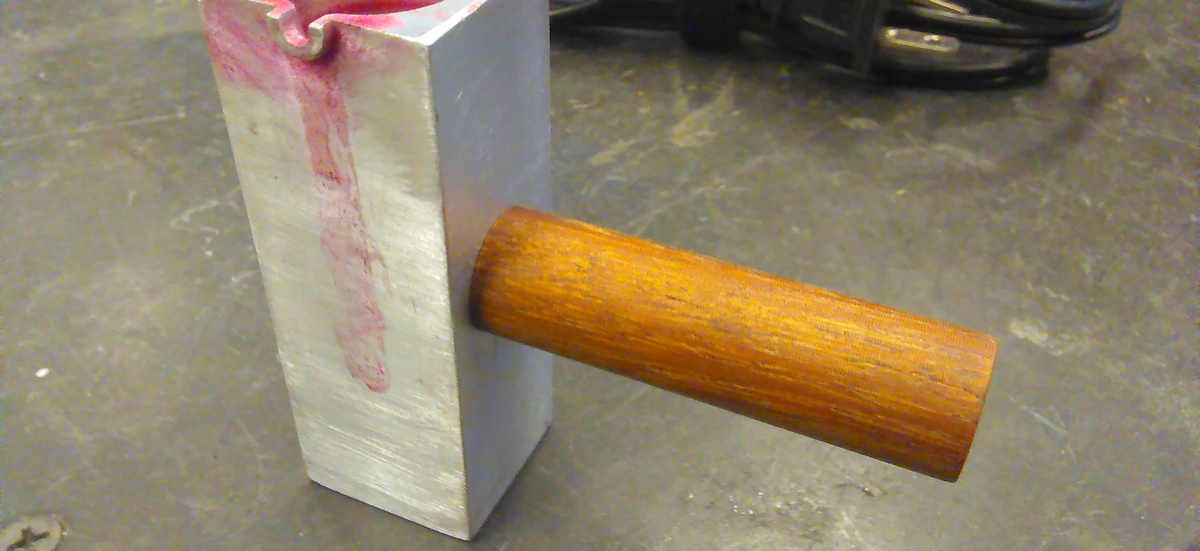
Description of Project
To create a better way to melt enough wax to create a wax seal with my custom bronze seal.
Processes Applied:



Summary:
The aim of this project is to create a method to melt enough wax to create a wax seal quickly and with ease. Currently, I am using a candle-based wax, whereby having a wick lit you produce a slow dribble of sealing wax. I occasionally thought about this issue over a few months but never came up with a decent enough design to spur me into fabricating it. One day I went about taking apart the hot glue pot that had been hanging from the MITERS door for over the last year or so. After disassembling the hot glue pot and realizing the whole thing was built around a small cartridge heater, a design quickly formed around the use of the same cartridge heater in a block of metal. Initially, I searched various websites (McMaster-Carr/Amazon/etc.) for cartridge heaters and tried to design around various models that I found... but in the end I decided to go the route of re-purposing the cartridge heater from the hot glue pot.
The design was simple, one hole in the bottom of the aluminum to press fit the cartridge heater into the base, One hole in the top to hold the volume of wax to be heated, and a spout for facilitating the pouring of the liquid wax. The bottom hole was drilled just slightly over the diameter of the cartridge heater, while also milling a small groove in the base to for the wires. Next, I drilled the hole on the top to hold the volume of the wax, It was important to me to leave a decent amount of distance between the base of the two holes ~.15"-.2". This was both to allow for a thermal mass other than the wax itself as well as decreasing the likelihood of puncture between the two holes. Once these two holes were made, I used a 2 part epoxy to fill in the hole below the cartridge heater. The epoxy was both rated for the temperature range as well as an insulator. The epoxy was used to both isolate the wires leading into the cartridge heater from one another, as well as adding a protective layer from any easy damage. After I had shown my friend Rob the initial final product, he pulled out some fancy mill tool holder. He suggested we use it to create a spigot-like feature. So with the use of this adjustable boring tool as well as a small mill bit and a fly cutter, we machined a spigot into the front side of the wax pot/heater.
Once I had machined these basic features into the bar stock of aluminum, I went about polishing up the surface of the material. The last important design consideration was a thermally insulating handle, I immediately chose a low-quality dowel rod off of the MITERS material shelf and drilled a two-step hole in it. This allowed me to use a simple bolt to mount the handle after I had finished it.
After a few days, a member of MITERS offered me a few pieces of nice scrap wood that she had acquired from a reuse post. These pieces were all square in nature, so I took a single piece and went about turning it into a rod on a lathe. Once I had done this, I went about replicating the design used for the previous handle. Finally, I finished the piece off with high grit sandpaper, and decided against using any dedicated oils for adding a finish. This was mainly due to the high quality of the wood, that I thought any real finish would take away from its natural beauty.